Victoria Fabricating
Custom Metal Driveway Gates | Custom Metal Railings | Custom Metal Staircases | Custom Structural Steel
CNC Plasma Cutting Victoria BC
In the dynamic arena of metal fabrication, precision, speed, and efficiency are non-negotiable.
One tool that stands tall in delivering on all these fronts is the CNC plasma cutter. If you've ever been curious about these game-changing machines, allow us to walk you through their prowess.
Here's everything you need to know.
CNC Plasma Cutters Unveiled
To start, CNC is short for Computer Numerical Control.
This technology grants machines the ability to work with surgical precision, all guided by a digital design.
The term "plasma" in our context represents the cutting mechanism at play.
When you combine the meticulous nature of computerized operations with the brute force of plasma, you get a beast of a machine that can carve even the most complex designs into metal with unparalleled accuracy.
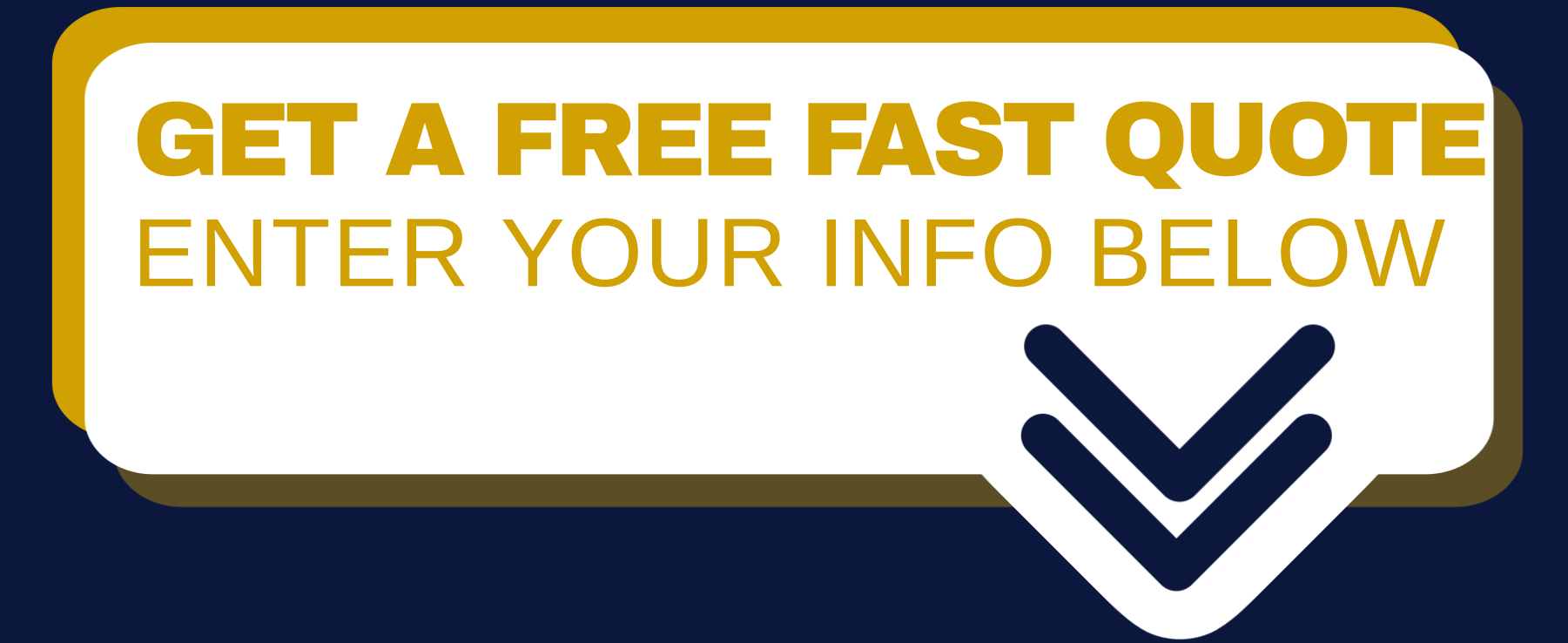
VFbr - CNC Plasma Cutting

At Victoria Fabricating, we're more than familiar with the groundbreaking potential of this technology. We've seen firsthand how it can revolutionize fabrication processes, making them faster, sharper, and more streamlined.
Decoding Their Functionality
Let's break it down simply: a CNC plasma cutter propels a stream of ionized gas, aka plasma, which allows an electric arc to form between the cutter's torch and the metal that needs cutting.
Given the intense heat of this plasma, it not only melts the metal but also ensures any residual molten metal is effectively removed. The result? A clean, sharp cut.
The applications of these machines are vast. From the auto industry to the world of construction, and even in artistic endeavors and bespoke sign-making, CNC plasma cutters are proving invaluable.
Their adaptability extends to a variety of metals — from common ones like steel, structural steel, and aluminum to more niche types like brass and copper. And thanks to the digital precision of CNC, the designs they can achieve are far beyond what traditional manual techniques could dream of.
Making a Case for CNC Plasma Cutters
If you're even remotely associated with metalwork or fabrication, here's why Victoria Fabricating believes a CNC plasma cutter might just be your next best investment:
- Precision Personified: With a computer at the helm, expect each cut to be on point. Consistency is the name of the game here.
- Optimized Output: Designed to run non-stop, these machines save precious time, ensuring quicker project completions.
- Diverse Capabilities: Their range extends from handling thick steel plates to delicate metal sheets. And when it comes to intricate designs, the sky's the limit.
- Economical Excellence: By ensuring precision, waste is minimized, leading to cost savings in the longer run.
- Safety First: Automation reduces direct human involvement, cutting down risks significantly.
Understanding Their Limitations
Though CNC plasma cutters come packed with advantages, it's only fair we discuss some of their limitations:
- Finishing Touches: While they cut with accuracy, the final edges might need a bit of refining, especially when held up against the likes of laser cuts.
- Material Restrictions: Their mainstay is conductive metals. So, materials like plastics, wood, or glass don't make the cut.
- Density Dilemmas: Super-thick materials might pose challenges. While they're adept for most tasks, when it's about extremely dense materials, you might need to consider alternatives.
Behind the Scenes
The brilliance of a CNC plasma cutter stems from a harmonious blend of its software and hardware components. It all begins with a digital design, generally crafted on CAD platforms. This digital blueprint then guides the machine's movements.
At the core of the operation is the plasma torch. Equipped with an electrode, it sparks an electric arc with the designated metal. This arc, in turn, heats up the chosen gas mixture (often a mix of elements like oxygen or nitrogen) to a level where it transitions into plasma. As this plasma gushes through the nozzle of the torch, it takes care of melting the metal. The movement of the cutter, under the vigilant guidance of the CNC mechanism, ensures the design is carved to perfection.
To sum things up, CNC plasma cutters, with their cutting-edge capabilities, have truly redefined the benchmarks in the fabrication realm. They are the embodiment of precision, speed, and efficiency. For those with an unyielding commitment to quality and a desire to push boundaries, these tools are indispensable. And when you have a trusted name like Victoria Fabricating backing your equipment, you're not just making a purchase; you're investing in a tradition of innovation and superior craftsmanship.
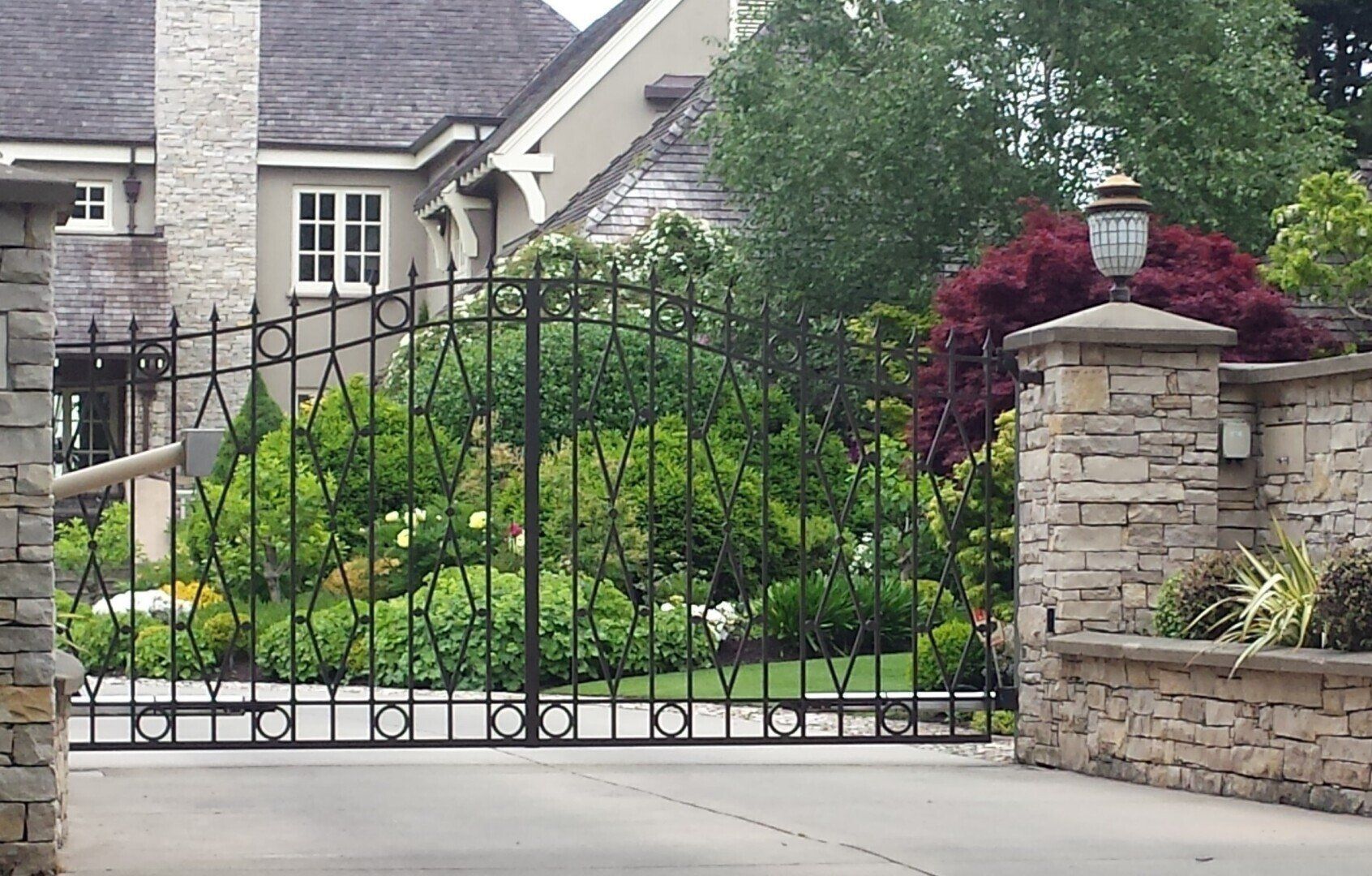
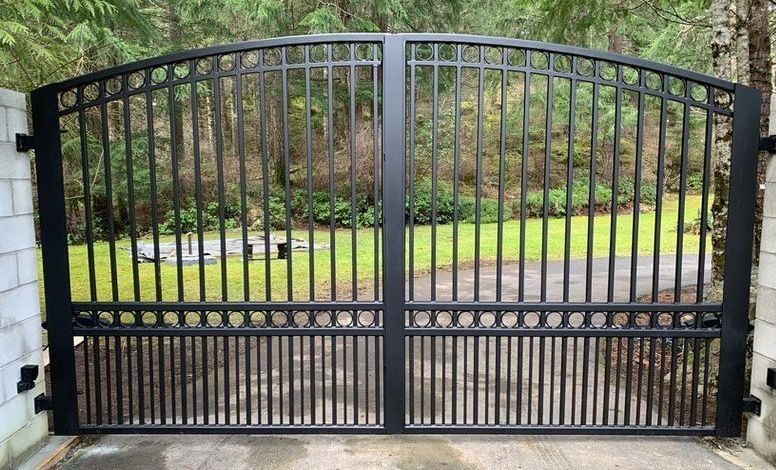